Recently, perforated panels intended for storing tools have become firmly established in various workshops. With their help, you can conveniently and compactly arrange any working tool in production or in a car repair shop. Also called cabinets or layouts, perforated panels have a design and functionality that allows you to arrange storage for any needs. They can be made from different material and are complemented by convenient layouts.
Perforated panels - description and materials
The panel is a sheet of wood-based material or metal with stiffening ribs along the edges and perforations on the working plane. These holes allow you to conveniently place and use comfortably tools, small-sized equipment, building materials.
Perforated layouts allow you to save money workplace, keep the necessary tool always at hand and control its availability. A workshop equipped with such panels will have modern look, and various working tools will always be at hand.
Perforated sheets are attached to special brackets, and tools are placed on them using holders, shelves and hooks. However, on sale you can find panel cabinets that are mounted without any fastenings.
Dimensions of sheets with perforation:
- On average, the height of such products is 200 centimeters and the width is 100 centimeters. Sheets with large dimensions can be produced for various workshops and garages. Their width can exceed more than two meters.
- The minimum layout size is 50 centimeters wide and 100 centimeters high.
- The thickness of wood-shaving sheets can be up to 7 centimeters, and metal ones - from 1 millimeter.
- The perforation diameter is 5 millimeters, and the distance between the holes is 15 millimeters. This allows you to fill the panel as tightly as possible and at the same time arrange everything conveniently.
- The step between the centers of fastening the hooks is 30 millimeters.
However, we must remember that the dimensions are calculated based on the overall dimensions of the product, while the working surface itself most often has rather modest dimensions. That is, with a structure height of 150 centimeters, the perforated surface used may account for only 50 or 100 centimeters.
Market building materials offers many different panel sizes, so there is plenty to choose from to fit any workplace.
The areas of application of perforated layouts are unlimited, however, for each case it is necessary to select product with certain characteristics:
- durable metal constructions well suited for professional workshops;
- small sheets will come in handy in a farmstead or garage;
- multifunctional layouts in the form of screens and modules are widely used in production and industry;
- Products with various additions have found their use in arranging display windows in hardware stores.
Affordable layouts for storing tools are easy to install and easy to use.
Advantages of metal products:
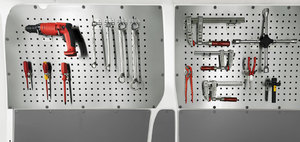
The most commonly produced are perforated panels in two colors. They can be white or natural wood.
The disadvantages of metal layouts include:
- Mandatory fastening for fixing a sheet of horizontal slats.
- Compared to MDF models, the price is quite high.
Perforated wood-based panels
When choosing MDF layouts, you should keep in mind that under conditions of increased use they are not able to provide adequate wear resistance.
Due to the low strength of the material, tool storage products are manufactured in small formats. Their standard size– 60x60 centimeters. Such layouts are quite durable, do not deform or bend. In addition, they are easy to transport and install in the right place.
Perforated MDF panels are designed for storing oversized tools only. With their help, you can conveniently place and operate hammers, spanners, screwdrivers, etc. At the same time, when choosing such products for your workplace, you must remember that when high humidity And high temperatures their service life will not be long.
Accessories for panels with perforation
It is rare that only a sheet with holes is enough to contain a tool. Therefore, most often, perforated layouts are sold complete with various holders and fasteners.

Methods for installing perforated layouts
The panels can be placed on various surfaces.
Wall sheets are the most popular type of design. They are fixed directly to the wall and secured with special screws. With the help of such layouts, you can save room space and, at the same time, comfortably use the work tool.
Perforated panels for mechanic's workbench are manufactured according to the length of the unit. Their size can be selected for a two-stand, single-stand or bas-stand workbench. The structures are fastened using special brackets and racks. In addition, two panels can be installed on the workbench at once.
In the middle of the room you can place modular screens or systems. They will also perform a zoning function.
Rear layouts can be conveniently placed on pipe stands or other suitable profiles.
It is worth noting that the placement of various additional elements depends on where and with what help the panel is installed.
Types of perforated panels
Layouts with decorative effect
To ensure an aesthetic effect, HDF perforated sheets are made from solid fibreboard. With their help, you can mask some interior items, as well as divide the room into separate zones.
These designs are different durability and decorativeness. No phenol is used in their production, so they are environmentally friendly. Wood-fiber material is able to cope with damp and any temperature influences, so layouts made from it can be installed in almost any room.
Sometimes it is necessary to move or transfer sheets of equipment to another location or room. The most convenient way to do this is with the help of special mobile layouts equipped with rollers or wheels.
Comfortable wall holder for tools, created with your own hands, any man will appreciate it. Such a device allows you not only to keep all the tools in sight and at hand at the same time, but also to keep them in order, while freeing up all working surfaces. How to make a similar board with magnets for your workshop or garage yourself, follow the step-by-step instructions.
Materials
To work you will need:
- boards;
- hot glue sticks;
- hook screws;
- heat gun;
- sharp knife;
- magnets;
- the instruments themselves.
Step 2. Adjust the boards to the parameters you specified and sand the cut areas.
Step 3. Place the boards on work surface. Prepare the magnets and the tools themselves.
Step 4. Do a rough fitting of where, how and what tools will be attached to the board. They should be located at a distance from each other so that while working, when you take any of them, you do not touch the neighboring ones with your hand. Consider mounting options for each tool.
Step 5. Mark the locations where the magnets will be attached with a pencil. Place magnets on hot glue.
Step 6. If everything is clear with small magnets for oversized and light tools, then to attach a row of screwdrivers you can take this long strip of magnets.
Step 7. To attach stationery knives in a plastic case, you will have to glue a small piece of magnets to them as well. Otherwise, the knives will not stay on the board.
Step 8. If you have tools whose metal can scratch the holder and cause serious damage over time appearance boards, like this caliper, attach a piece of heat-shrink tubing over the magnet. Take a more powerful magnet itself.
Step 9. To attach a mini spotlight that is used during soldering or other minor works, place it with its base on metal plate and screw it to the board with self-tapping screws.
Step 10. Attach a set of drills and bits to hooks for convenience. When purchasing them, pay attention to models whose fastening ends are similar to self-tapping screws.
Step 11. Place a long flat metal ruler on several small magnets at once, placing them at a short distance from each other.
Step 12. It is a little more difficult to secure a saw with an aluminum handle, since aluminum is less magnetic. To do this, you will have to modify the saw a little by riveting onto it metal part.
Step 13. In order to keep on vertical board heavy screwdrivers, attach them to neodymium magnets or pieces of magnetic disks. They are much more powerful than ordinary ones, and will cope with this task.
Perforated panels are necessary for organizing work in garages, workshops and car repair shops. They successfully complement bedside tables with shelving to achieve the best ergonomics in the workplace. If you place the tool that is used most often above the workbench, then you will no longer have to rummage through drawers in search of the necessary things. The technical equipment can also be hung back quickly and conveniently after use. At the same time, at the end of the working day, it is visually clear that since the hook is empty, it means the key was lost or left, for example, in the car during the repair process. We need to find it and hang it back. We recommend using perforations even if the equipment is stored in a cabinet. During renovations, when you change various fixtures, a mess is involuntarily created on the countertop. If you hang everything you work on on hangers, the surface is freed from unnecessary items. Hanging a key is much more convenient and faster than constantly putting devices in drawers. The holders hold not only the tool, but also Consumables. So, for example, in the case of electrical work, all kinds of terminals, casings, and electrical tape are hung up, and when doing embroidery, it is very convenient to store a set of threads on the panel. Doing your favorite hobby brings more pleasure manual labor provides additional comfort when the workplace is in order.
The perforated shield can be installed on or attached to the wall with self-tapping screws. Especially for this purpose, its dimensions correspond to the length of non-pedestal, single-pedestal and double-pedestal models. The screen is attached to the table with special stands and brackets. Installation of one or two panels is possible. The cutouts on the panel flange are made in such a way that it can be hung horizontally and vertically, which helps to optimally fill the area, bypassing existing communications and terrain.
Wall mounting is quite simple. There are 4 figured cutouts on the back side. 4 screws are screwed in, and then the panel is hung on them, like Wall Clock. You can make markings before drilling using any thin sharp nail or awl on the front side.
The hole pitch is 15mm. This allows you to fill the shield as completely as possible necessary tool. The distance between centers is 30mm. The diameter of the holes in the perforated screen is 5mm. For screwdrivers, grips, and other small items, special
. Wall perforation< выпускается двумя сериями. "Лайт" наиболее популярна за-счёт отпускной цены. У серии «Стандарт» толщина металла больше, соответственно выше стоимость, но и нагрузочная способность существенно выше. Данную модель используют для размещения тяжелых вещей.
Products are painted polymer coating, immune to temperature changes and aggressive substances.
Many thematic forums on the Internet are full of reports on how to restore order using a perforated panel. With us, your wish will come true. We will help you solve specific problems.
Perforation loads
Perforated panel length | 1000mm | 1390mm | 1900mm | |
Perforation hung on the wall | Series "Standard" | 68kg | 60kg | 60kg |
Series "Light" | 55kg | 50kg | 50kg | |
If the perforation is mounted on brackets on a workbench, the distributed load is 100 kg. |